1872年、チャールズグッドイヤーは、簡単に分解できる高耐性の靴が製造できる機械を生み出しました。 これは当時の靴市場に革命をもたらし、この縫製方法に彼の名前であるグッドイヤーと名付けました。
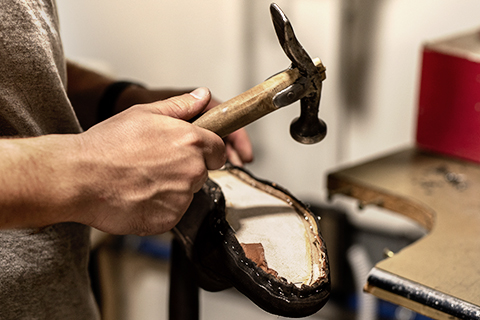
グッドイヤーステッチは耐久性のある靴作るための最も手間のかかる方法です。(そして私たちカルミーナが得意とする製法です。)機械を操り、多くの手作業を必要としますが、どの工程においても熟練した職人が必要です。 このプロセスには120以上の異なるステップがあり、靴を作るのに最短でも4日が必要です。
それでもグッドイヤーウェルト製法の多くの利点の1つ、耐久性を得るためには無駄な時間ではありません。そして、上質な 革はあなたの靴に呼吸をさせ、敷き詰められたコルクはあなたの足型に完全に適応し、快適さのポイントを追加します。 こうした特徴的なプロセスの積み重ねによって、比類のない耐久性と履き心地を提供する事ができます。


グッドイヤーウェルト製法のシューズが特別で、多くの専門家に高く評価されている理由は何でしょうか。 その秘密は二度のステッチにあります。
魔法は、パターンの精緻化と最高の革の選択から始まります。 カルミーナでは、高品質の製品を提供するためには、高品質の材料を使わなければいけない事を知っています。 そして、各モデルの「アッパー」がどのように形成されるか、つまり靴を形成するアッパーレザーのピースがどのようの組み立てられるかを知り尽くす必要があります。
しかし、この製法を本当に特別なものにしているのは、ソールの取り付け方法です。
まず、アッパーとインナーソールとウェルトを一度目のステッチで縫い合わせます。 幅が約1.5cmの革のウェルトは、底面をぐるりと囲む360º、またはヒールからヒールまでの270ºの二つのタイプがあります。 ウェルトの取り付けが済んだ後、職人が余分なアッパーを切り取ります。
次はコルクの詰め物です。 これにより、靴のインナーソールは数日の使用で足裏に適応し、パーソナライズされた快適なフィッティングを提供します。 カルミーナの職人は、インナーソールとアウトソールの間のスペースに詰める独自のコルクペーストを開発しています。 また、かかと部分には金属製の芯の入ったシャンクを入れ、ステップの安定性を高め靴の構造を強化します。
最後に、二度目のステッチでアウトソールを取り付けます。
アウトソールはウェルトに縫い付けられ、ヒールをセットするベースになります。 この段階で、アウトソールを取り付けるために2度のステッチが施されています。一度目はアッパーとインナーソールとウェルトと結合し、2度目のステッチでウェルトとアウトソールが結合せれています。 つまり、アッパーにダメージを与えることなく、アウトソールの交換が可能になりました。
これにより、正しいケアと可能なメンテナンスを維持している限り、靴の耐久性を大きく伸ばすことができます。また、アウトソールのステッチとインナーソールのステッチが独立しているために、インナーソールまでダイレクトに水を吸い上がることが無く、足をよりよく保護します。
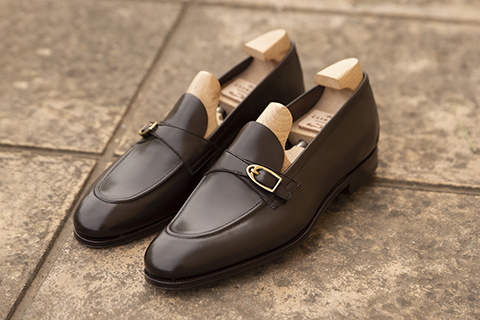
さらに、カルミーナでは、豊富な経験に基づき研究を進め、更に軽量のグッドイヤーウェルトシューズ 「ソフトウェルト」ラインのシリーズを開発しました。